Forust gives wood waste a second life through 3D printing
- Oct 17, 2021
- 3 min read
Updated: Aug 7, 2023

_TECHNOLOGY
LOCATION: USA
Forust, a new company of Desktop Metal, has released a first-of-its-kind, high-speed 3D printing technology that upcycles wood waste and repurposes it into beautiful end-use products.
To showcase the revolutionary printing breakthrough, Forust partnered with Swiss industrial designer Yves Béhar, founder of fuseproject, to design the very first exclusive collection of home goods - Vine. The Vine collection includes a vessel, bowl, basket, and tray - perfect for adding a naturalistic feel to your home and for storing those easy-to-misplace items.
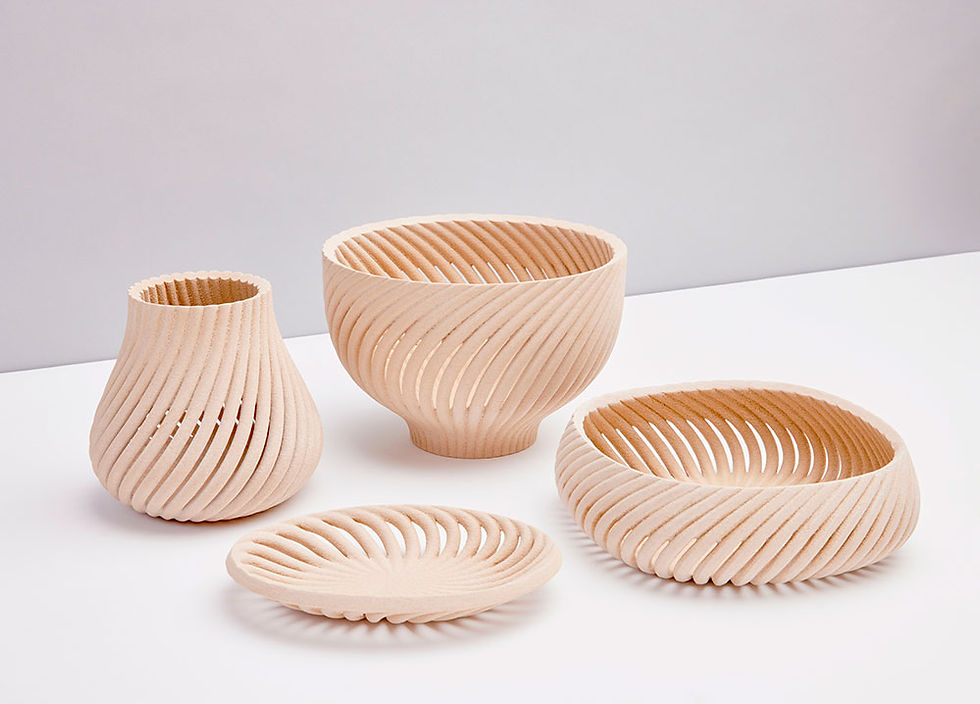
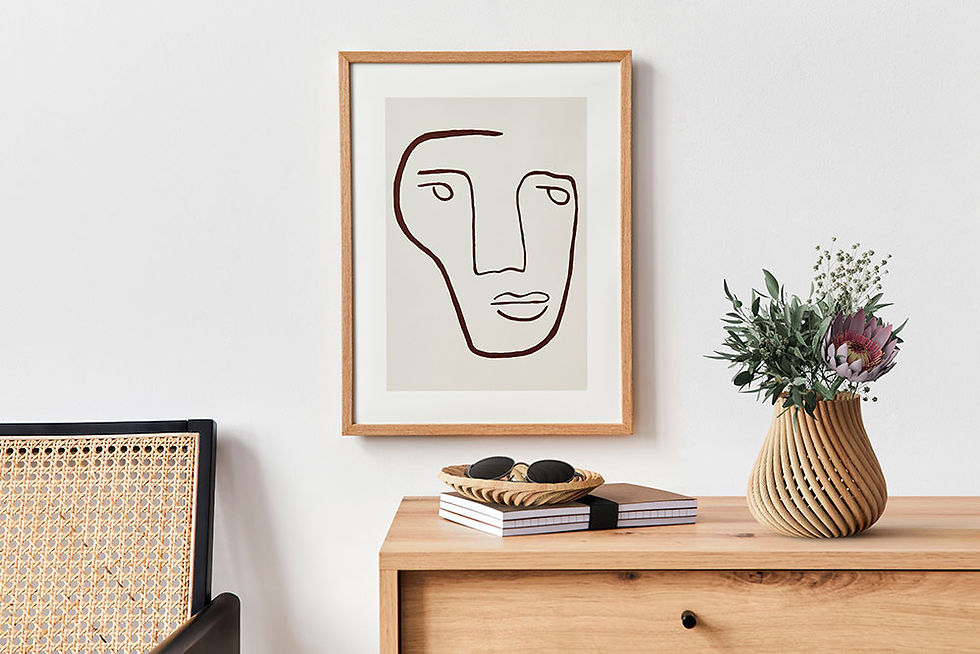

The process
The technology you're looking at lies within the domain of 3D printing technology, but the Forust process is very different from the common conception of 3D printing.
In its most popular forms, 3D printing or additive manufacturing typically squirts out molten plastic in layers to build up a finished part, and sometimes different kinds of materials are introduced like metals or woods combined with plastic (PLA).
The gamechanger in the Forust process is the introduction of a new type of material into the system that does away with industrial thermoplastics altogether and instead uses natural waste materials.
The Forust process upcycles two waste byproducts from wood manufacturing - sawdust and lignin (a natural polymer found in the cell walls of woody plants) to sustainably produce isotropic, high-strength, wood parts.
During the printing process, thin layers of specially treated sawdust are spread and selectively joined by a non-toxic and biodegradable binder to turn them into wood.

The most interesting part is that “digital grain” can be printed onto every layer and parts can then be sanded, stained, polished, dyed, coated and refinished just like real wood.
The Forust process has the ability to mimic almost any wood grain, from Ash to Zebrano, Ebony to Mahogany and achieve a strength that the company claims is similar to conventional wood.

Building a greener future through 3D printed wood
Forust was born with the aim of recycling wood waste into usable end-use products.
Every year, approximately 15 billion trees are cut down to produce paper, build homes and make furniture. From this, millions of tons of wood are generated annually. While a portion of this is recovered to make particle board or wood pellets for energy, the remainder is sent to landfill or incinerated.
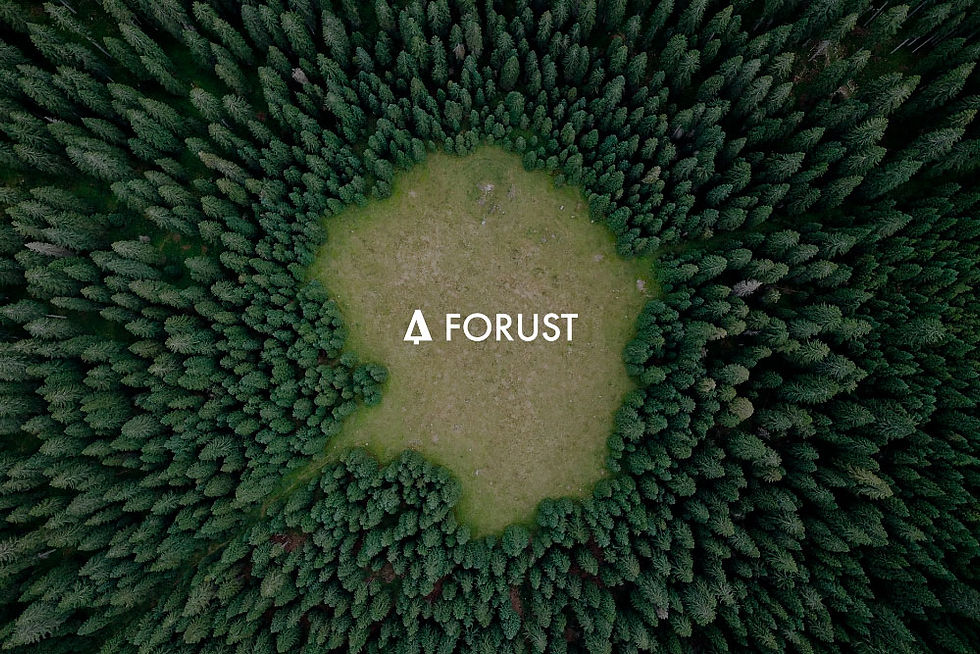
Although sawdust is biodegradable, Forust points out on their site that sawdust can be harmful to the environment in large quantities when landfilled. Burned wood waste contributes to air pollution. "As it decomposes, sawdust releases high concentrations of lignin and fatty acids, which can contaminate water supplies, potentially poisoning wildlife and micro-organisms," explains Forust.
Forust is essentially changing the cycle of wood waste by diverting the waste from our landfills and waterways and upcycling the wood waste into architectural elements, consumer & home goods, furniture, and more.
Waste reimagined
Forust is expanding the design possibilities of making things out of wood with no waste.
By creating objects additively layer by layer, Forust can make any shape or form offering architects, designers and manufacturers a new path to explore complex new geometries and designs that would be difficult or impossible to produce with traditional woodworking methods.

Forust can be used for almost anything, from consumer products, furniture, home goods, architectural accents, consumer electronics, instruments, aviation, boats and interior and exterior elements.
The applications for Forust’s wood parts are really limitless, and is really up to the designers imagination.

To learn more about Forust, visit www.forust.com
Sustainability Advantages
Upcycling Forust transforms two waste by products from wood manufacturing - sawdust and lignin - to produce isotropic, high-strength, sustainable wood parts. Reusing waste materials takes far less energy, water, chemicals and other resources required to make new virgin materials.
Less waste Additive manufacturing is the basis behind 3D printing. Instead of removing material, it “adds” material layer by layer so that only what is required gets used. It generates significantly less waste than traditional subtractive manufacturing methods since material doesn't need to be cut away and discarded.
Comments